Производство сборных железобетонных конструкций на заводах
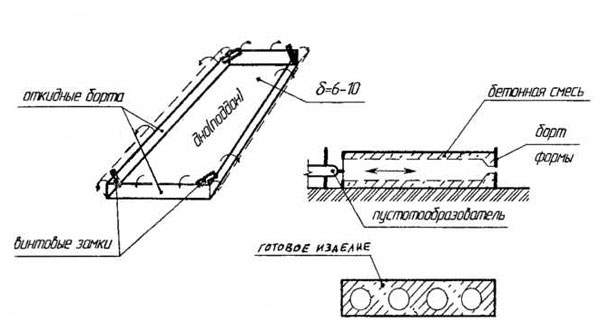
Заводы железобетонных конструкций (ЖБК) или изделий (ЖБИ) имеют мощности от 10 до 300 тысяч кубометров железобетона в год. По видам изделий различают:
— универсальные заводы ЖБК, выпускающие широкую номенклатуру изделий: плиты, балки, колонны, фермы и т. д., а также поставляющие бетонную смесь (товарный бетон) и арматурные изделия;
— специализированные заводы ЖБК, выпускающие конструкции лишь одного вида: трубы различного диаметра, опоры линий электропередач (столбы) различных размеров, конструкции мостов, железнодорожные шпалы и т. д.
Завод включает:
— основное производство: формовочные цеха и камеры ускоренного твердения бетона (пропарочные камеры);
— вспомогательное производство: бетонный завод (узел), арматурные цеха;
— складское хозяйство: открытые склады песка и щебня, силосы с цементом, резервные емкости с водой, закрытый склад арматурной стали, открытый склад готовой продукции;
— путевое хозяйство: как правило, завод имеет подъездные железнодорожные пути для поставки материалов (песок, щебень, цемент) и отгрузки готовой продукции, сеть внутризаводских автодорог.
Завод оснащен высокопроизводительным технологическим и мощным крановым оборудованием. Заводы ЖБК являются крупными потребителями электрической и тепловой энергии, поэтому их располагают вблизи ТЭЦ или в их состав включают собственные котельные.
Состав процесса такой же, как при устройстве монолитных конструкций, но имеет ряд особенностей.
Опалубка используется стальная, многократно оборачиваемая (50–200 раз) и называется формой (рис. 5.1). Это достаточная прочная конструкция, которая имеет откидные борта и мощные запоры на них. Форма каждый раз подготавливается к бетонированию: очищается от налипшего бетона предыдущего цикла и покрывается эмульсионной смазкой (рис. 5.4, п. 1).
При изготовлении сборных железобетонных конструкций применяются обычные арматурные изделия (сетки, каркасы), а также напрягаемые элементы арматуры (стержни, высокопрочная проволока, пряди).
![]() |
Рис. 5.1. Стальная форма для изготовления пустотной плиты |
Изготовление обычных арматурных изделий производится в арматурных цехах, оснащенных высокопроизводительным стационарным оборудованием: машинами для контактной стыковки и резки, для гибки прутков; сварочными автоматами и полуавтоматами, в т.ч. многоточечными (рис. 5.2), а также мощными подъемно–транспортными механизмами.
![]() |
Рис. 5.2. Механизированные линии по изготовлению арматурных изделий: а – сеток; б – каркасов колонн |
Процесс изготовления арматурных изделий включает:
— правку проволоки;
— стыковку прутков в непрерывную плеть;
— разметку прутков или проволоки;
— резку по размеру;
— гнутье элементов (при необходимости);
— сборку арматурных изделий.
Все эти процессы выполняются раздельно (рис. 5.3) или комплексно на механизированных линиях (рис. 5.2).
Стержневые элементы напрягаемой арматуры нарезаются заданной длины. Проволоку и пряди при натяжении используются в бухтах (мотках) и после заданного натяжения использованная часть отрезается от бухты.
В подготовленную к бетонированию форму укладывают арматуру и закладные детали. Но перед этим производят натяжение закрепленной в форме предварительно напрягаемой арматуры для создания в изготавливаемой конструкции сжатых зон в заданном месте. Этот прием позволяет перераспределить напряжения в бетоне конструкции и сократить расход стали на 20-40%. Натяжение ведется электро-термическим способом (удлинение стержня при разогреве током) или механическим натяжением тонкой проволоки домкратами (рис. 5.4, п.2).
![]() |
Рис. 5.3. Изготовление сетки на одноэлектродной контактно–сварочной машине |
![]() |
Рис. 5.4. Технологический цикл изготовления железобетонного изделия (плиты): 1 – подготовка формы; 2 – установка арматуры; 3 – укладка бетонной смеси; 4 – уплотнение смеси на виброплощадке; 5 – тепловая обработка в пропарочной камере; 6 – извлечение из камеры и распалубка; 7 – подача изделия на склад; 8 – отгрузка изделия на объект |
Затем производится бетонирование конструкции с подачей бетонной смеси передвижным бетонораздатчиком (рис. 5.4, п. 3). Стальная форма (опалубка) вместе с забетонированным изделием краном подается на вибростол (рис. 5.4, п. 4), где производится объемное уплотнение бетонной смеси.
Процесс выдержки в заводских условиях обеспечивает не только нормальный набор прочности бетона, но и значительно сокращает его время. Вместо нормальных 28 суток здесь бетон набирает 70% расчетной прочности за 6–12 часов. Это обеспечивается термовлажностной обработкой изделия в пропарочных камерах (рис. 5.4, п. 5).
Пропарочные камеры бывают трех типов: ямные, туннельные, колпаки.
Ямные камеры: большое подвальное помещение глубиной от 1 до 6 м, шириной от 4 до 20 м и длиной от 20 до 100 м, открытое сверху. В него краном загружаются забетонированные изделия вместе с формой (устанавливают друг на друга штабелями). Помещение закрывается крышкой и в него подается пар (рис. 5.7, а; п. 3). Динамика изменения температуры (нагревание, прогрев, остывание) регулируется подачей пара и контролируется автоматически.
После завершения пропаривания крышка с камеры снимается, изделия вынимаются краном и подаются на склад готовой продукции. Затем цикл повторяется (рис 5.4, пп. 6 и 7).
Туннельные камеры. Представляют собой напольный туннель длиной 30–80 м, внутри которого по рельсам перемещаются формы с изделиями. Торцы туннеля закрыты мягкими брезентовыми пологами. Внутрь туннеля подается пар, тепловой режим контролирует автоматика. В отличие от
ямного типа тепловая камера работает непрерывно, без остановок на загрузку изделий. Однако в этом случае расход пара выше за счет неплотностей в торцах камеры.
Тепловые колпаки. Представляют собой коробчатые конструкции каркасного типа, устанавливаемые на ровную площадку кверху дном (типа корыта). Предварительно на эту площадку складируют в штабеля формы с изделиями, затем их накрывают колпаком. Размеры колпака: ширина 3–6 м, длина 12–18 м. Под колпак подается пар и проводится пропаривание изделия (рис. 5.7, б; п. 3). После окончания тепловой обработки колпак снимается, и изделия подаются на склад. Цикл повторяется. Достоинства: малые начальные затраты (не надо капитальных камер). Недостатки: большой расход пара, малая долговечность колпака (недостаточная жесткость и прочность при подъемах).
Виды производственных технологий. В зависимости от организации процесса изготовления изделий используют в основном два вида технологий: агрегатно-поточную и стендовую.
Агрегатно-поточная. Все процессы и операции выполняются на специализированных рабочих постах, оснащенных высокопроизводительным оборудованием: сварочным, вибрационным, тепловым и т.п. Форма (с изделием) пооперационно перемещается вдоль постов с помощью мостового крана или рельсовой тележки (рис. 5.4).
Достоинства: высокая производительность, возможность быстрой переналадки на другие размеры или типы изделий.
Недостатки: размеры (до 6–9 м) и масса (до 3–6 т) ограничены параметрами виброплощадок, большой расход пара.
Стендовая технология. Все процессы и операции выполняются на одном месте – в пропарочной камере. Поэтому частично используется переносное оборудование (вибраторы, бетонная бадья).
а) длинные стенды. Служат для изготовления ферм длиной 18, 24, 30 м в положении «плашмя». Форма на всю ферму стационарная и находится на дне пропарочной камеры глубиной 1,0 м. Здесь производятся все операции: очистка и смазка формы; натяжение арматуры; установка обычной арматуры и закладных деталей; бетонирование (подача бетонной смеси бадьей и уплотнение глубинным вибратором). Далее камера закрывается, изделие пропаривается и после снятия крышки извлекается из камеры краном. Следует отметить, что для ферм тепловая обработка ведется до достижения бетоном 100% расчетной прочности.
Достоинства: возможность изготовления длинномерных конструкций.
Недостатки: сложность переналадки на выпуск других изделий, большая продолжительность процесса (нельзя одновременно задействовать много людей);
б) короткие стенды (кассеты). Специальное оборудование для производства несущих железобетонных стеновых панелей в вертикальном положении. Оно представляет собой пакет плоских стальных емкостей (тепловых панелей), которые могут горизонтально перемещаться по направляющим. В собранном пакете пространства между емкостями служат формами для стеновых панелей. В них устанавливается арматура (сетка) и формы заполняются литой бетонной смесью. Одновременно с бетонированием включаются расположенные снизу вибраторы и уплотняют бетонную смесь в форме. Затем в тепловые панели подается «острый пар» при давлении 5–10 атм. и температуре 110–120°С. Такая температура значительно повышает эффективность тепловой обработки и сокращает сроки твердения. После завершения прогрева секции последовательно раздвигаются и из них краном извлекаются готовые изделия. Далее цикл повторяется.
Достоинства способа: высокая производительность, малые затраты пара. Недостатки: вся система пригодна лишь для изготовления одного типа изделия.
Источник: Технология строительных процессов. Снарский В.И.